FIVE TIPS TO AVOID COMMON FMEA MISTAKES
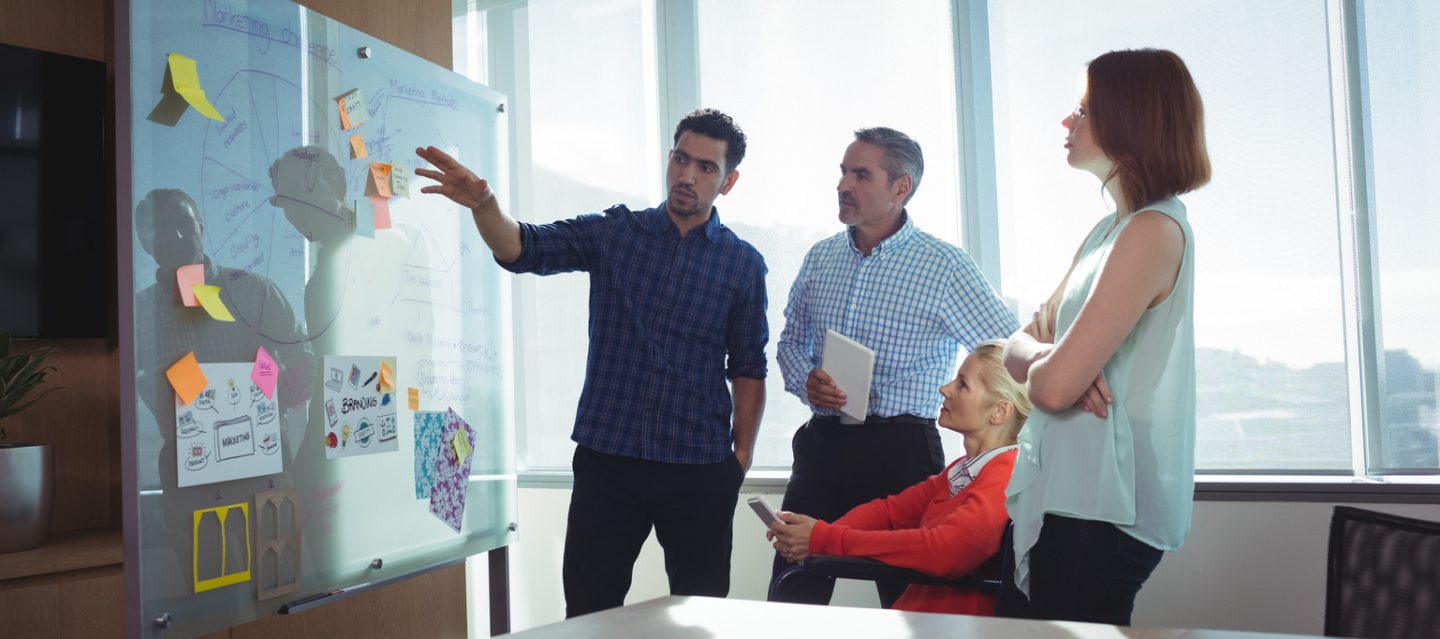
Over the past 40 plus years in my career as a Risk Practitioner, Quality Manager, Trainer, and Consultant I found myself on a continuous basis working on customer reported product compliance issues that would cost the organization millions of dollars annually. Approximately 50% of all the incidents had absolutely nothing to do with product non-compliance but, instead improper installation of the products shipped to our end customer’s assembly operations. The other 50% traced back to these four FMEA performance deficiencies;
- FMEAs that did not consider all possible failure modes,
- FMEAs that contained severity/occurrence/detection ranking values that did not correctly represent operating conditions,
- FMEAs that lacked applicable, and effective preventive/mitigative actions, and
- FMEAs that documented high-risk items with excellent recommendations not followed through to closure.
I recently found an interesting (DesignNews) web article titled “5 Tips to Avoid Common FMEA Mistakes” by Greg Jung that summarises very succinctly the primary reasons we still have ineffective FMEAs at many of our workplaces to this day. It is my sincere hope that by sharing this article, you will not have to go through your career forced to handle the types and level of pain, worry, and daily stresses that I did during my career. I have added my thoughts and experience comments to each of the five tips and sincerely hope that you enjoy the richness of the author’s insightful tips as much as I have! If you are responsible for your company’s risk management program, you may want to download the full paper from the author which I have provided the URL for at the end of this blog.
As I started reading, my head automatically began nodding up and down in agreement with the author’s declarations. You have heard the saying Been there, Done that! That is what was going through my mind. The truths written by the author made me feel like, this guy had been videotaping my career.
Having worked as a Quality Manager in the automotive parts manufacturing arena for 20 plus years, I was under the gun to update FMEAs and Control Plans on an almost daily basis. My company was on the low end of the supplier food chain which meant trying to satisfy what seemed to be ever-changing product design and performance specifications just days before new product launch due dates. Sure enough, the author of this article states the first common mistake as being performing FMEA’s too late in the Design Cycle.
In automotive parts manufacturing, we knew that changes would come late in the design development stage, so we would deliberately attempt to hold-off completing FMEAs and Control Plans until we just couldn’t hold off any longer. Here’s the author’s first tip.
-
Performing FMEA’s Too Late in the Design Cycle
“Many teams will procrastinate, starting their FMEAs until well after the design is established and mature. Unfortunately, this delay greatly reduces the effectiveness of FMEAs because simple changes that could have been implemented upfront are now difficult to incorporate because the design has become more rigid (or even frozen) Instead, try to begin FMEAs before the concept design or process is created. This will establish an earlier reliability framework and allow for improved upfront trade-off decisions and more meaningful feasibility studies. Getting an earlier start on FMEAs will have a more positive overall impact on the product or process design.”.
The author’s experiences match identically with mine in automotive parts manufacturing. I found throughout my career that last-minute product design changes put my company behind the eight ball every time. These last-minute changes exposed our organization to costly rushed tooling, process, and documentation changes. Despite our best efforts to satisfy the customer last minute changes, resulted in reported issues, unfair ridicule, and expensive audit scrutiny.
One way that I found significantly helps in handling these last-minute changes was to have a flexible and scalable risk software solution that enables rapid documentation changes ensuring linkages between FMEA, PFMEA, Control Plans, and other applicable shop floor work instructions. It is critical to make sure all connected information is correctly updated and communicated to all associates in the organization who need to know. This strategy requires investment in people, processes, and system, but the investment is a preventative must have if your business needs to adapt quickly to changes. The pace of change in the automotive industry will keep going faster with more electronics, cybersecurity, and other competitive forces in the market.
Well, lets now look at the author’s second tip to making FMEAs more effective.
-
Not Including System Interfaces in the FMEA
“Many teams do an excellent job of properly detailing individual part or subsystem failures, but forget to include the system interface failures that occur between these parts or subsystems. These interface considerations are critical because a large percentage of total failure modes usually occur at these interactions. When performing FMEAs, remember to increase the scope of the analysis to always include all interface and integration failures in both the block diagrams and the failure mode lists.”
Again, the author nails it! Having the right people with the right skill sets on your risk assessment team is key to making sure that all potential failure modes will be considered and evaluated in the context of being required to interface with other internal and external systems that may include both hardware, software, and firmware. I have found the best way to ensure interface issues get considered in the risk assessment, is to make sure the team includes stakeholders from all areas of the business affected by potential consequence outcomes of failure. Team leaders must have the appropriate senior management support to permit personnel from any area of the company, including suppliers, and customers. They can be critical to diagnosing potential interface shortcomings between your product and other systems invisible to the companies risk assessment team.
Additionally, it is essential to have a risk software solution that has an open APIs to provide linkage with PLM, ERP, and other systems that store master data need to conduct risk assessment studies. Keeping data consistent and linked from BOMs, DFMEAs, PFCs, PFMEAs, CPs, and Work Instructions is critical managing change quickly. Without an IT strategy for connecting master data into your risk assessments studies you will repeat the four issues, I identified in the first paragraph of this blog.
It is also critical to make sure that documented high-risk items found through studies are followed through to closure. So many companies complete studies without systems to assign and track preventive and mitigative actions. You must track and monitor that actions are being taken on time to prevent and mitigate risk.
I was impressed with this article because it included the effective use of empirical field failure data which is a key ingredient that gives FMEAs integrity.
This leads us into the author’s third tip being,
-
Field Data Not Connected to FMEA
“Historical field data contains a wealth of actual failure knowledge that can be translated into FMEAs. Unfortunately, many companies overlook this valuable data and don’t properly link their evaluations to actual field failure data and previous lessons learned. Create more effective FMEAs by incorporating all major historical field data such as field recalls, high warranty failures and excessive spare parts usage. Following this practice will dramatically improve future product performance and help ensure that field problems are not repeated.”
I have found companies that take the appropriate time to investigate, document, and turn their field failure data into valuable FMEA library information end up spending far less time in team meetings debating the severity, occurrence, and detection values. Of course, these libraries are only useful if the data within them has been accurately validated through careful examination and closed-loop root cause analysis methods.
Let us now move on to the author’s fourth tip being,
-
Not Having the Right People or Commitment
“Training and experience count when producing effective FMEA’s. Properly trained teams composed of the right experts who are highly engaged and regularly attend meetings will produce the best results. Use of cross-functional, multi-disciplined team members is also important because diverse teams will uncover more hidden failure modes due to their varied perspectives. Strong upper management commitment to the FMEA process and a highly knowledgeable facilitator/trainer should also be present to ensure successful results and the most effective use of resource time.”
As a Technical Training Instructor for an automotive parts manufacturing, I have seen radical differences in the quality and usefulness of countless FMEA studies. The sad reality is that I was sent out into the field to assist global sister plants in resolving relatively simple issues that cost several hundreds of thousands and even millions of dollars annually. Upon examination at these problematic locations, I found FMEAs that had what I call the white pages. They were called white pages because there were very few or no preventive/corrective actions identified or assigned on the righthand side of the FMEA. They were prime candidates for concern and the reason why costly failures occurred at the worst possible times at these companies. In short, FMEAs completed by team members without the appropriate drive or risk training are easily identified by experienced risk assessors. Deficient FMEAs are easy to identify due to their incompleteness, inaccurate data, rankings that don’t match the ranking definitions. Not to mention may have zero to very few actions assigned to reduce identified risk items. The importance of making sure the right people are on assessment teams should not be left to chance. Risk team leaders that take the appropriate steps necessary to ensure the integrity of the FMEAs produced by their team members will never be out of work.
One last tip to discuss the fifth,
-
Creating More Effective FMEAs
“In addition to avoiding these common mistakes it’s also important to properly prioritize the evaluation efforts up front. Start by focusing on the highest risk areas first such as: new designs/technology, safety issues, field history problems, and any other critical design characteristics. Remember to always be risk conscious and to develop higher amounts analysis detail in the higher risk areas of the design or process. By applying all of these simple guidelines throughout the entire development cycle, your FMEAs will become more effective and produce a more reliable product with the most efficient use of your time.
While Failure Mode and Effects Analysis (FMEA) is a very effective method for driving reliability and quality improvements, when used improperly, this tool can also result in unidentified root causes, inadequate actions or misguided efforts. Too often FMEA issues occur because simple guidelines and best practices were not followed throughout the entire development process.”
I agree with the author’s statements throughout this article. For me, the quality characteristics of a well done and effective FMEAs consist of some pretty simple principles that I found over the years to be essential ingredients that separate difference between non-effective and effective FMEAs.
- FMEAs should drive product design or process improvements as the primary objective.
- The FMEA should address all high-risk failure modes with effective and executable action plans.
- Design Verification Plans (DVP) and Process Control Plans (PCP) need to consider and identify control methods for each of the failure modes identified in the applicable FMEAs.
- The FMEA scope needs to include integration and interface potential failure modes analysis.
- FMEAs should be able to generate “lessons learned” that can be used to prevent future repeat of failures.
- Causes of failure in FMEAs need to be analyzed at the root cause level to know that controls in place are and will be effective in preventing similar and future repeat failures.
- FMEAs need to be conducted at appropriate life cycle stages and be inter-linked to next stages to feed the appropriate risk information required to effectively conduct the next stage of life cycle analysis.
- Successful FMEA teams utilize the right people with the knowledge and training required to ensure all potential failure modes are considered and adequately evaluated to ensure the best possible controls are in place to minimize corporate liability.
- The best Preventive and Corrective Actions are only effective if they are fully implemented and result in reducing the level of severity and or likelihood of failure.
- Actions that provide only improvement in failure detection levels are a waste of corporate funds because they do nothing to reduce the number of potential failure events that will occur but, rather only makes one more aware they actually happened.
You may want to download the full paper from the author if you are responsible for your company’s risk management program. The URL is: https://www.designnews.com/design-hardware-software/5-tips-avoid-common-fmea-mistakes/146084881646624
I am always interested in learning more about how our reading guests and software solution users are dealing with the core issues included in this article. I am sure there are things we could (or already have done) within our software to help improve FMEA studies. However, if you have any additional thoughts about where you see bottlenecks or have any other comments, I invite you to please reach out to me at pmainprize@sharrix.com
Leave a Reply